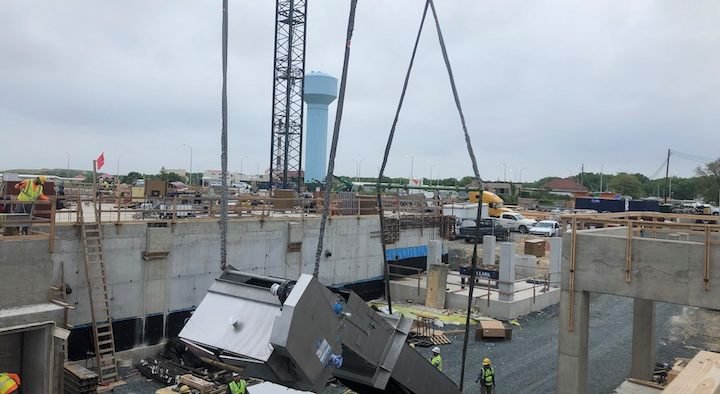
Ullman Schütte strives to provide customers with a high-quality end product that is delivered on time and within budget.
When Ulliman Schutte Construction LLC builds a project as a general contractor, it looks for ways to complete portions of the job on its own. This “helps us control the schedule and quality,” Kristina A. Bruns says. “It also leads to highly accurate scheduling and estimating.”
Bruns is the senior project engineer and quality control manager for the Miamisburg, Ohio-based company, which builds and renovates water and wastewater treatment plants and pump stations, and performs associated utility work. “We want to provide our customer with a high-quality end product that was delivered on time and within budget,” she says.
Ulliman Schutte is currently bringing these best practices to its Back River Headworks project in Baltimore. The company partnered with Clark Construction on the $429 million project, which consists of a new headworks facility, equalization facilities and other plant improvements.
Baltimore, which will use the facility to eliminate sewage and unwanted discharge, has needed the facility for a long time. “They needed to meet the EPA requirements to get the capacity they needed,” Bruns recalls.
On Its Own
Ulliman Schutte and Clark started on the headworks facility two years ago and are working towards an operational Headworks Facility by Dec. 31, 2020 to meet the EPA’s consent decree requirements. The contractors need to “get the facility in operational to meet the consent decree requirement,” Bruns says.
Like on its previous projects as a general contractor, Ulliman Schutte is completing much of the work on its own, about $80 million’s worth. This consists of coarse screens, 70,000 GPM influent and equalization pumps, fine screen facility, grit removal facility, odor control facilities and other ancillary process systems.
Bruns says she is proud of Ulliman Schutte’s work on the project, including how it has quickly found solutions to schedule constraints. One example was how Ulliman Schutte helped build the facility’s influent pump station.
At the time, the project team wanted to place the roof on the building, but needed to install the large pumps first. “We were able to create a solution to meet their requirements,” Bruns says.
“In order to make that work, we have had to fly these pumps down through the structural steel,” she recalls, adding that the company used a gantry system to move the pumps into place once inside the building. The pumps weighed 35,000 pounds, so this was harder than it sounds. Ulliman Schutte then worked around the schedule of the roofing contractor to complete its work.
Under Pressure
Lessons Ulliman Schutte has learned during the headworks project include how to move forward even when it encounters restrictions on a job of this size. “It’s the largest projects I’ve ever worked on,” Bruns admits.
“It’s about finding ways to meet constraints and working with our vendors and pushing things along,” she says. The company also met the critical challenge of staying safe, Bruns notes.
So far the entire project has achieved over 1 million man-hours without incurring any lost-time injuries. “All the subcontractors have done a great job of being safe, including ourselves,” she says. “Safety is the No. 1 priority for the entire team.”
Bruns particularly praises the work of Horton Mechanical, a subcontractor that is completing the Odor Control Facility. “We have used them on previous jobs where we’ve been the general contractor,” she says.
Big Believers
A seven-year veteran of Ulliman Schutte, Bruns credits its success to its strict focus on water and wastewater projects. “Because we don’t branch outside of that, we’re able to bring proven ideas to our clients and design partners,” she says.
“These ideas consist of ways of improving quality and enhancing operability. We’re big believers in improving all aspects of our projects, including cost, for all stakeholders.”
The company’s focus on customer service also has earned it a strong base of repeat clients, including DC Water and its Blue Plains Advanced Water Treatment Plant. “That really makes us stand out from our competitors,” Bruns says. “We go into a job hoping we get repeat business. That is our end-goal with a project.”
Bruns sees growth ahead for Ulliman Schutte, which wants to reach new customers. While the company currently serves clients in North Dakota, North Carolina, Virginia, Washington, D.C, Maryland, Kentucky, West Virginia and Ohio, “We’re always looking at other states to expand to,” she reports. “Everyone needs clean water.”
Enhancing Skills
Ulliman Schutte provides training to enhance its employees’ skills. For example, new engineers undergo internal online training models to become more familiar with the company’s methods. Facilitated, third party training is also offered on a broad arrange of topics focused on leadership and career growth.
“I’ve done [those] personally and found them very helpful,” Bruns says, noting that she also took a U.S. Army Corps of Engineers Quality Control course. “Before I got into this position, they helped me learn what I needed to be successful.”